
RYAN LAFROMBOIS
ASME R/C Baja
Suspension, Chassis & Steering
Proposal Presentation - Fall
Working Device Presentation - Winter
Final Presentation (PART 1) - Spring
Final Presentation (PART 2) - Spring

About ASME RC Baja Challenge
The ASME R/C Baja challenge allows senior level engineering students to work in teams to design, build, and manufacture vehicles to compete in a competition. An additional requirement is the creation of a website to document and present progress of each students part of the project. This website represents the suspension and chassis half of the build which will work in unison with teammate, Connor Donovan's powertrain. The suspension and chassis are critical parts of the project as it contains all components and sets the powertrain up for success.
Motivation
This project was motivated by an interest in R/C car construction and custom suspension geometry. Other motivations involved in this project is a passion for automotive custom construction, previous R/C vehicle experience, and an interest in manufacturing.
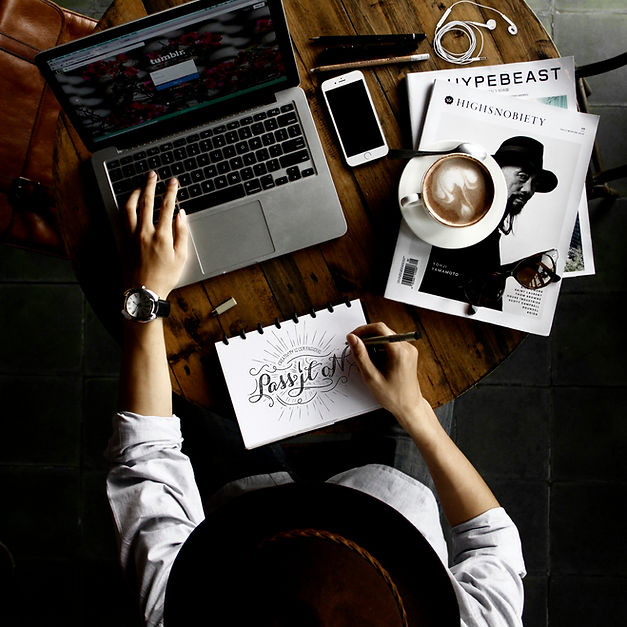

Figure 1
Front end independent cantilever concept drawing.
​
​
*does not feature rear suspension and steering
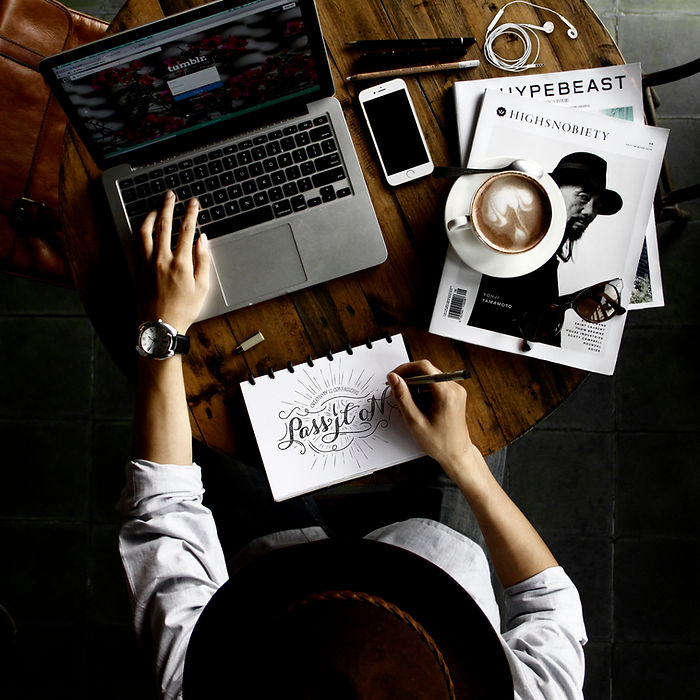
ALTERNATIVE DESIGN #2
Independent cantilever design.
*From web design assignment 1*
​
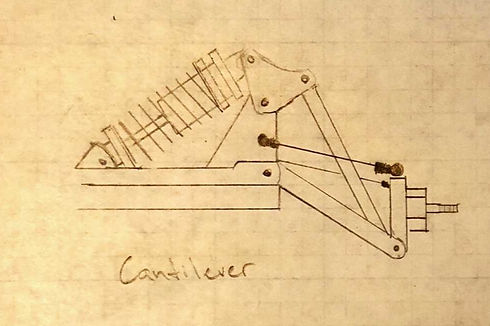
RESULTS
The evaluation of the RC Baja device during the spring quarter featured three main tests. The tests are documented in the testing section and the report document.
​
The first test was the turn radius test which was conducted in the Hogue Fluke lab. The predicted result for this test was 2.5-feet and the actual result was 1.5-feet. This result was much better than the predicted value as it would allow the team to be more successful in the slalom event. The second test was the chassis deflection test which was completed in the Hogue Machine Shop using the materials available. The predicted value for the test was .100-inches and the actual value was .044-inches. This result was again, much better than the team had predicted which improves the rigidity of the device overall. The last test was the 2-foot drop test which was completed in the Hogue Fluke lab. The device was evaluated on whether or not the chassis plate would impact the ground. The predicted value was that the chassis plate would impact the ground due to the change in suspension springs to opt for the softer choice. The test showed that the drop did result in the chassis contacting the ground which fails the requirement. The reason for the change in springs was the product of an engineering decision as the stiffer spring would make the forces on the other components could cause them to fail.
​
Overall, the device met the all but one of the criteria and performed exceptionally in the competition. Based on the testing evaluation and the competition performance, the team has decided that the device was a success in the chassis, suspension, steering, and drivetrain.